Dieser Artikel ist noch nicht auf Deutsch vorhanden
Selecting the right detergent for the cleaning of your process equipment
Inhalt
Cleaning-in-place involves the jetting or spraying of surfaces and the circulation of cleaning solutions through the plant under conditions of increased turbulence and flow velocity. According to the principle of Sinner’s Circle (figure 1), efficient and successful cleaning requires the presence of 4 essentials components: mechanical/kinetic energy (turbulence), thermal energy (sufficient high temperature), cleaning time and chemical energy (chemical reaction of the detergent chemicals with the soil). While a deficiency in one of the energy components may be partially compensated for by an increase in one or more of the other factors, all four are vital to the total cleaning operation. As cleaning time is aimed to be kept as short as possible and as temperature is often limited for reasons of safety, mechanical action and the detergent chemicals to select remain the only variables left to play with within the whole cleaning process.
In CIP-processes, the flow velocity of the cleaning liquids in piping with an internal diameter of 10 cm is usually kept at 2 m/s. Larger flow velocities give no beneficial cleaning effect, increase pipeline pressure losses due to pipe friction and demand larger pump power. Moreover, to large pressures near the spraying devices can increase the risk for atomisation of the cleaning liquid, reducing to zero the impact of the cleaning fluid on the vessel wall to clean. Therefore – on the exception of hygienic equipment design and several other methods to apply mechanical action (pigging, liquid vibration and pulsation, …), the cleaning power of the detergent chemicals remains the only factor left to improve the cleaning efficiency and to reduce the cleaning time.
Selecting an adequate cleaning agent
A cleaning process can be considered to consist of three primary steps: (1) the displacement of organic and/or inorganic soil from the equipment substrate, (2) the dispersion of the soil into the cleaning medium and (3) the prevention of soil redeposition on the substrate. The first step demands a cleaning agent with an excellent wetting power to reduce the surface tension of the cleaning medium and to help the cleaning liquid to penetrate into the soil and surface pores. The solubilisation of the soil can be increased thanks to the property of the detergent chemicals to disperse and sequester respectively the organic and inorganic soil. The second step requires detergent chemicals with excellent suspending and emulsifying power to bring the insoluble soils into suspension and to hold oils and fats dispersed within the cleaning solution. To finally prevent the redeposition of the soil, the dispersing and sequestering properties involved in the first step are addressed again.The selection of an adequate process cleaning agent is a demanding task. Apart from the cleaning result which varies from physically clean over chemically clean to microbiologically clean, the risk for detergent residues in food and pharmaceuticals produced after the cleaning process, the food-grade character of the detergent chemicals, their compatibility with the equipment substrate, their environmental and operational impact, and their safe application become more and more important. Different steps have to be followed in the selection of an optimal detergent formulation for your cleaning process. In a first step, the desired level of cleanliness, the plant design and construction materials, the cleaning techniques available, the type of soil present, the manner in which the soil is formed, the nature of the production process and the chemical composition of the water supplies have to be defined. In the following step, a subjective selection has to be made based on technical knowledge, written documentation and the product specifications of the CIP-detergents available on the market. Thirdly, the detergent formulations who survived the first rough selection can be subject of laboratory trials, where coupons made of the same material like that found in the process equipment are used as test sustrate to clean. These coupons with sufficient surface roughness must be covered with the soil type that has to be removed, and are subjected to a standardised cleaning process. In the fourth step, process components having a history of difficult cleaning can be subjected to the small number of detergent formulations that survived the former laboratory trials. Finally, operational aspects like cleaning efficiency versus cost and services after sales delivered by the detergent supplier are determinative factors in the final purchase of that detergent formulation found to be suitable for your CIP purposes. But, although the selection process is then finished, the quality/validation engineer has to struggle further through a time-consuming and laborious ‘cleaning validation’ process. Not one process component has to be validated, but all process components within the factory are part of the validation process. Especially in pharmaceutical plants subjected to regular FDA-control, ‘cleaning validation’ is a demanding job that must be produced in three fold.
Technical knowledge and written documentation as basis for a subjective selection process
To fulfil the cleaning task, a detergent formulation usually consists of an alkaline (for organic soil removal) or an acid (for inorganic soil removal) substrate, supplemented with one or more surface active agents (to enhance the wetting power of the cleaning medium, and to help in dispersing and emulsifying the soil), one or more builders and sequestering agents (to increase the cleaning efficiency of the surface active agents and to prevent the precipitation of calcium and magnesium salts onto the equipment surface), corrosion inhibitors, antifoaming agents, oxidising agents, …
Inorganic alkalis
Most alkaline detergent formulations use NaOH as basic ingredient. Sodium hydroxide has good powers of detergency for fatty-type soils and protein deposits by virtue of its ability to form water-soluble chemical products following a chemical reaction, in e.g. the hydrolysis of fat or the peptisation of proteins. Although the cleaning power of potassium hydroxide equals that of sodium hydroxide, and in spite of its better rinsability characteristics, the use of KOH in cleaning practice is not as common as that of NaOH. The price level of potassium hydroxide is much higher than that of sodium hydroxide, making it economically less favourable for application in the food industry. But, in the pharmaceutical and biotech industry, the better rinsibility of potassium hydroxide often outweighs the aspect of cost, increasing its use in this area of the consumer industry.During their use, caustic alkalis are gradually converted to carbonates, causing scale or bloom to appear on equipment and utensils. In that case, sodium orthosilicate, sodium metasilicate and trisodium phosphate are very effective for removing heavy soil without risk for blomm formation and corrosion. In wetting power, soil lifting power, dispersion and emulsification power are these compounds even superior to NaOH and KOH. But in reality, most important detergent suppliers make no or rarely use of sodium orthosilicate, sodium metasilicate and trisodium phosphate; and if the detergent formulation contains a phosphate-typecleaning agent, then sodium tripolyphosphate and sodium hexametaphosphate are preferred for their supplementary sequestering and water softening effect. Only in neutral cleaners with a pH from 6 through 8, are NaOH or KOH replaced by sodium carbonate, sodium bicarbonate, trisodium phosphate, sodium tripolyphosphate, … giving mild alkalinity and buffering capacity to the cleaning solution. To obtain more wetting and emulsifying power, surfactants are supplemented to these neutral cleaners in addition to dispersants, corrosion inhibitors, … Neutral cleaners are rather used in these circumstances where sodium hydroxide based detergents have a corroding effect, e.g. on aluminium, galvanised and other soft metal surfaces, … Contact of NaOH with such materials does not only lead to rapid corrosion, but induces also the release of hydrogen gas which can form an explosive mixture with air.
In the food industry the alkalis NaOH and KOH are required in 95% of all applications for their chemical reactivity: to hydrolyse the present hydrophobic compounds like fats and proteins into more hydrophilic ones. In the pharmaceutical industry in contrary, the demand for these alkaline compounds is less severe. Although even these, most detergent suppliers subscribe the use of NaOH and KOH for several reasons: firstly, the development of special caustic free detergent formulations for a small market segment like the pharmaceutical industry is economical not interesting; secondly, NaOH and KOH have a certain microbiocidal effect; thirdly, scale formed during the alkaline cleaning cycle is usually removed in a second acid cleaning cycle; and fourthly, the removal of hydrophobic organic materials (e.g. lubricants, oils, … remaining after a maintenance check-up) sticking onto the hydrophobic vessel wall is always assured. Moreover, a high alkaline environment helps the surfactants to penetrate the soil more readily.
Surface active agents
Surface active agents are always present in detergent formulations. Their main task is wetting, soil penetration, soil suspension, dispersion and emulsification. Further, they help in the rinsing of the equipment surface by reduction of the surface tension. As the surface tension of water is 72 mN/m compared with 52 mN/m for milk and 43 mN/m for beer, the presence of a surface active agent is to allow the cleaning solution to penetrate into crevices and capillaries within the surfaces to be cleaned. There is however no direct relationship between the ability to reduce the surface tension and the cleaning ability, because the cleaning properties of surfactants are also largely determined by such factors as size and concentration of the micelles and the compatibility of the surfactants with the soil.Non-ionic surfactants are most frequently used in detergent formulations, because anionic surfactants are highly foaming. Cationic surfactants have rather low detergency but high biocidal properties. In combination with non-ionic surfactants, amphoteric surfactants are sometimes supplemented for their microbiocidal effect.
For cleaning applications in the food industry, two or four different surfactant types are quite acceptable, but for pharmaceutical cleaning applications, limitation of that number of surface active agents to only one compound is recommended. Large numbers of detergent compounds in a detergent formulation can disturb the pharmaceutical profile of a final product (with detergent impurities). This is especially true for those cases where this final product is applied in intravenous dose forms.
Another point to keep an eye on, is the biodegradability of the surfactants present in the detergent formulation. Bad biodegradability increases the COD-load of the water purification plant. In the worst case a lack of biodegradability can trouble the waste water de composition process, e.g. when waste water contains very high COD-loads and when the oxygen supply is insufficient or too low.
Complexing agents
Other compounds ofter supplemented in detergent formulation are complexing agents. They act as a builder, enhancing the cleaning effect of the surfactants (e.g. polyphosphates, borates, citrates). They work within alkaline cleaners in strictly stoichiometric ratios as real complexing agents improving the removal of inorganic soil (e.g. EDTA, NTA, gluconate), or they are active in substoichiometric concentrations as sequestering agents (threshold agents) having the additional property to prevent the disposition of water scale on equipment surfaces during the rinse cycles (e.g. phosphonates, polyphosphonates, polyacrylates). During the rinse cycles, the remaining film of the cleaning solution on equipment surfaces is diluted and reduces the concentration of the classic complexing agents EDTA and NTA. Since rinse water is invariably hard – unless WFI (Water For Injection) is used – the power of the classic complexing agents is greatly reduced and residual alkalinity on surfaces causes the surplus water hardness to precipitate. With sequestering agents like phosphonates, polyphosphonates and polyacrylates, the formation and growth of calcite crystals is disturbed or the water hardness crystals are dispersed.Apart from the complexing agents mentioned above, several other complexing agents are used in detergent formulations. Although the detergent formulation is usually proprietary to the detergent producer, for the user sufficient information about all compounds present in a detergent blend can be of utmost importance (especially in the pharmaceutical/biotech industry).
Experience has taught that certain detergent formulations can contain compounds that are rather foreign to common food and pharmaceutical/biotech prepartions: e.g. polymeric and co-polymeric substances, amino trimethylene phosphoric acid, phosphono butane tricarboxylic acid, NTA (nitrilo tri-acetate), DTPA (diethylene triamine penta-acetate). Although the food industry is less critical than the pharmaceutical/biotech industry regarding detergent formulations, the ‘E-additives’ list of the European community seems to be a useful guideline in selecting a food-grade detergent formulation. Moreover, in the pharmaceutical /biotech industry, formulations with only one or two compounds are more preferable than multi-component blends. Therefore, blends adapted for use in both the food and pharmaceutical industry are rare. Detergent suppliers rather possess a specific portfolio of detergents well adapted for application in the food industry, or they are specialised to fulfil the needs of the pharmaceutical industry. Nowadays, several detergent producers start recognising these different and specific needs of both the food and pharmaceutical/biotech industry. Therefore, detergent producers (begin to) develop a specific gamma of cleaning agents for each of these industries.
Oxidising agents
To enhance the cleaning effect of an alkaline detergent formulation, hydrogen peroxide can be supplemented during the cleaning process. NaOH and H2O2 react with each other during the CIP-process concomitant with the development of oxygen. This oxygen generation can start up a local microturbulence which helps to improve the cleaning process. But, as concentrated NaOH and H2O2 are explosive on mixing both at high temperatures, attention has to be paid to the safe handling of these chemicals. Before mixing, these chemicals have to be diluted at low temperature in the CIP-tank, or they have to be injected separately into the CIP supply line by two dosing pumps. Hydrogen peroxide guarantees a fairly perfect cleaning, but the risk for chemical attack on rubber and plastic components present within the process installations is a major drawback. When the use of H2O2 cannot be excluded, optimisation to low percentages of H2O2 is ofter a prerequisite.Corrosion is often the main reason for not using a detergent in common cleaning practice. Therefore, other oxidising agents like hypochlorites that cause pitting on stainless steel and taint pick-up with certain plastics, are rarely applicable. To prevent the corrosion of stainless steel by detergent chemicals, corrosion inhibitors like (poly)silicates, modified carbohydrates and phosphonates are usually added to the detergent formulation.
Antifoaming agents
Foaming is another important characteristic to be controlled. Too much foaming has a negative impact on cleaning efficiency, and the time taken to rinse the equipment free of detergent rises dramatically. As a consequence more rinse water has to be used. Moreover, foam can also affect the level control equipment, can cause severe damage by cavitation in centrifugal pumps and can contribute to drag-out because of its tendency to cling to surfaces. Therefore, foam development has to be controlled with defoamers. Non-ionic surfactants can work as defoamers by their ‘cloud point’ effect. These molecules become insoluble above a fixed temperature, and separate from solution. Silicones are also excellent defoamers, but they must be avoided due to their tendency to adhere to surfaces very tenaciously.Acid cleaning agents
An alkaline cleaning cycle is usually followed by an acid cleaning cycle. Acids are usually used for the dissolving of mineral salts or for the removal of scale formed after an alkaline cleaning cycle. However, CIP processes in the fermentation and brewery industry are mainly based on acid cleaning practices, as CO2 generated during the fermentative process will rapidly break down the NaOH present in alkaline cleaning agents to Na2CO3. These sodium carbonates can quickly precipitate as process-generated scale, while the loss of CO2 can create an underpressure within the fermentor, increasing the risk for reactor implosion.Although some detergent suppliers are not afraid to advise the use of 1% hydrogen chloride (E507) cleaning solution in combination with the use of cationic corrosion inhibitors, the risk for pitting the stainless steel is much too high to recommend its use for daily practice. Especially in those cases where the equipment is heated or dried at high temperatures, corrosion spots due to local accumulation and concentration of chlorides with time have to be feared. However, in enamelled process equipment the use of hydrogen chloride cleaning solutions poses no problems and is even beneficial to the enamel structure. On the contrary, the NaOH used during the alkaline cleaning cycle is aggressive on enamel, but the subsequent HCL cleaning cycle helps to restructure it.
1-2% nitric acid cleaning solutions are useful in the cleaning and demineralisation of heat exchangers and evaporators, although nitrous vapours can pose risks of skin burns and hamper operators in their activities. Moreover, nitrates (together with phosphates) contribute to the eutrophication of the surface water.
In its raw form, sulphuric acid is corrosive towards stainless steel and should be formulated with a corrosion inhibitor, if regular use is envisaged. Sulphuric acid (E513) (in 1% solution) is the cheapest source of acidity, but its inherent detergency is poor and not cost-effective. The application of sulphuric acid in cleaning practice is also limited to 40°C. Sulphuric acid can be used in some sanitizer formulations in which the low pH is a prerequisite for effective use of the biocide present. Major drawbacks of sulphuric acid: sulphates contribute to the salt loading of the effluent, and under aerobic conditions high levels of sulphate cause physical damage to the concrete walls of the waste water treatment plant. Water purification plants with an anaerobic treatment step can also give rise to H2S formation, even at low sulphate concentrations. Therefore, more acceptable and common in cleaning practices are phosphoric acid or organic food acid cleaning solutions.
Phosphoric acid (E338) is of course quite acceptable, but, when frequently used, a significant increase in the phosphorous waste water load can occur. Moreover, for reasons of eutrophication, many countries demand supplementary taxes per unit phosphorous wasted in the envirionment. As few food processing companies have a P-removal step available in their waste water treatment plant, phosphoric acid is often replaced by organic acids like formic acid (E236), acetic acid (E260), citric acid (E330), tartaric acid (E334) and the less common acid cleaning agents lactic acid (E270) and gluconic acid (E574). All of them are much less aggressive than mineral acids, and are generally accepted in food practice. But their use largely depends on factors such as food cleaning efficiency and waste water load. Formic acid, acetic acid, citric acid and tartaric acid will increase the COD-load of the waste water. Although they are quite biodegradable, it cannot be ignored that large amounts of these acids can trouble the degradation of waste water effluents rich in organic material of low degradability. In most cases however, these problems can be ascribed to the insufficient treatment capacity of the waste water plant and to a shortness in oxygen supply needed for the degradation of the waste load. Other analogous acids that can be found in detergent formulations are glycolic acid and hydroxyacetic acid. These acids are however not listed on the positive ‘E-list’ of the European Community. Although, one can sometimes also place question marks near some compounds in the ‘E-additives’ list of the European Community, e.g. biphenyl (E230) or orthophenylphenol (E231).
An acid oxidising agent regularly used in cleaning practice, is peracetic acid. Peracetic acid is highly reactive, making it an excellent detergent and disinfectant. Moreover, peracetic acid is non foaming and therefore very suitable for CIP. However, peracetic acid has an irritant smell, and it may attack plant materials such as rubber gaskets. At higher concentrations, corrosion may be a problem. The biomass in the water treatment plant can also suffer from too high peracetic acid loads.
Detergent selection
Laboratory trials for objective selection
On laboratory scale, a subsequent more objective selection can be performed on coupons made of the same material like that found in the process equipment to be cleaned (in nearly all cases 316 stainless steel). These coupons with sufficient surface roughness (better fouling adhesion) are covered with the soil type that has to be removed, and are subjected to a standardised cleaning process. The cleaning effect of a detergent formulation against a certain soil type can be monitored by several means. Alternatively the weight loss of the coupons covered with a certain soil type can be monitored in function of the cleaning time, or the soil load of the cleaning solution in function of that cleaning time can be registrated.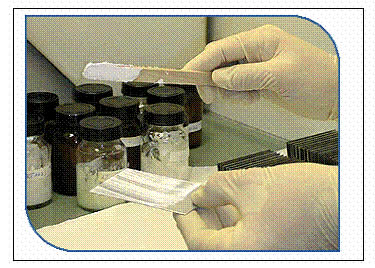
In the first case, each coupon is weighed prior to use. The surface of the tared coupons is then uniformly coated e.g. by dipping in the soil solution or by bringing an exactly quantified amount of soil on the coupon by means of a pipet or another aid.
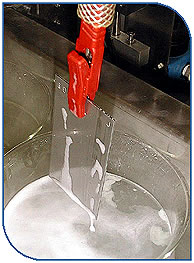

To maximise soil adhesion, the coupons have to be dried for a predefined time at room temperature or at the inner equipment temperature. This procedure can simulate the real circumstances ofter happening in empty production equipment where the soil dries on the equipment walls. The dried coupons then have to be weighed again, and the net dried soil must be determined. Each dried coupon can then be immersed in several beakers with the same detergent solution.
The water must be allowed to completely cover the coupon, and circumstances. In a CIP process, with increasing cleaning time every equipment part makes contact with a cleaning solution of lower soil load. This is especially true for CIP-processes without any recovery of the cleaning solution, where the first cleaning solution removes the largest part of the soil and – because the soil layer on the equipment surface diminishes with cleaning time – the soil load in the subsequent cleaning solution systematically decreases with that time. At the end of the run, the coupon is dried and weighed again. The weight loss corresponds with the amount of soil removed and can be expressed in µg/cm2.
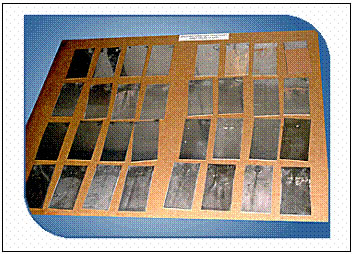
The second procedure proceeds very analogous, but in this case the soil load in the cleaning solutions is determined e.g. by TOC analysis.
Industrial scale trials
Industrial scale trials as ‘real process circumstances’ selection toolIn the following selection step, the small number of detergent formulations that survived the ‘coupon’ selection test can be test on process parts that the production managers – based on their practical experience – have evaluated as being very difficult to clean. These industrial scale trials are very important, as the test results obtained with coupons can differ remarkably from the results obtained from the tests with these equipment pieces. Moreover, the presence of seals makes it possible to screen for corrosion and crimp effects.
To monitor the cleaning process several strategies can be followed. The weight loss of the test pieces (loss of soil) can be monitored in function of the cleaning time; the soil load of the cleaning solution in function of that cleaning time can be registrated (e.g. by TOC analysis); or the soil remaining on the equipment can be swabbed from the equipment surface, extracted from the swab with water and then accurately analysed by TOC analysis.
Further, a detergent formulation found to be perfect for your cleaning job must guarantee a quick free rinsing of your cleaned process equipment. Therefore, tests on a laboratory or industrial-scale should also be performed to screen for detergent residues left on the process equipment. For this purpose, TOC analysis can be used as a non-specific method monitoring the amount of these detergent residues left behind on the cleaned surfaces. Detergent residues are swabbed from the surface, extracted from the swab with water and then accurately analysed for organic carbon by TOC analysis. The amount of detergent residue can be expressed as µg/cm2. First swab recovery studies are needed to determine the percentage recovery with a specific swab. Moreover, the reproducibility of swabbing and the TOC-test method have to be evaluated.
‘Challenge tests’
‘Challenge tests’ to evaluate detergent substrate compatibilityThe detergent that is finally preferred for the defined cleaning task should not corrode or physically damage the construction materials.
Although the compatibility of the detergent chemicals with the materials used in the construction of the process plant has to be determined at the earliest opportunity, to prevent costly damage to these capital items, difficulties in the removal of the soil often force the process manager to use just these detergent chemicals (e.g. peracetic acid, hydrogen peroxide, sodium hypochlorite) that can have detrimental effects on the construction materials. In that case, substrate compatibility tests always have to be performed. For that purpose, materials (coupons or equipment pieces) can be immersed for several days or weeks into a detergent solution of certain concentration (e.g. 5%), at the objective cleaning temperature. During and at the end of this period of immersion, the samples in 304 or 316 stainless steel, aluminium, zinc, copper, brass, tinned and galvanised materials, neoprene, viton, silicone rubber, Teflon and EPDM can be rinsed, dried and evaluated as to appearance, weight change, thickness and hardness. Detergent formulations where – during this long period of exposure to high detergent concentrations – all materials present in your process installation remain free of any corrosion or physical damage, can be evaluated as being safe for use.