
tecnología > lubricación en alimentos > uso > cervecería |
This article is not yet available in the language you selected
Food grade lubricants in the brewery
Article index
Science overcoming trouble brewing
Brewing beer; an art or a science? The Brewer's Handbook1 describes brewing beer as "really a very simple process, a unique mix of art and science" and many would argue that careful selection and malting of barley and the judicious selection and use of hops lend more credence to brewing as being an art. However with the globalisation of beer brands and beer manufacture, science is increasingly playing an important role in brewing. In terms of the beer manufacturing process, the science of lubrication is having a major impact.As a food processing industry, brewing has been forced somewhat to choose between risks to quality and their brand reputation and plant efficiency. Desiring to reduce the risk of contamination some breweries and equipment manufacturers switched from long proven non food grade lubricants to white oil based H1 compliant lubricants where lubricants can come into incidental contact with beer or its components during the manufacturing process. However equipment manufacturers then began seeing reduction in equipment component life of as much as 75%. The development of synthetic food grade lubricants, complying with the NSF H 1 standard is quickly removing the dilemma of product quality risks versus productivity and plant down time.
Lubrication Contamination
Lubrication Contamination Control Point (LCCP) systemModern brewing companies are adopting processes to analyse and reduce risk of contamination in their manufacturing process. The HACCP System (Hazard Analysis Critical Control Point System) is a system stipulated by the EU2 to be used in food production and by the FDA in an increasing number of food industries.
In any HACCP system lubricants are considered as chemical hazards and can either be monitored or removed as a hazard. Modern lubricant suppliers offer as part of their service a Lubricant Contamination Control Point (LCCP) audit. The LCCP follows the HACCP methodology and focuses on lubricant contamination.
Equipment manufacturers and plant designers, which build modern brewing facilities, will ensure that lubricants do not come in accidental contact with the food components of beer manufacture. When this cannot be done in the design of the new facility, nor economically re-engineered an existing facility, the best option is to use a H1 compliant food grade lubricant.
Keeping moving metal parts separated, cleaned, corrosion free and cooled is only part of the role of lubricants. In a brewery environment, wherever there is potential for contamination of product, NSF H1 approved or complying lubricants must be used. Traditionally, NSF H1 lubricants were formulated using “white oil” base fluids. White Oils have the most desirable lubricating characteristics removed to comply with food contact requirements. Additives used were traditionally limited to “zinc” based and as a result, performance of these lubricants was less than satisfactory.
For these reasons, many breweries have specified non-food grade lubricants where they can to attain enhanced machine performance. However they then risk that lubricants which are not H1 compliant will come in contact with beer or its components during the manufacturing process.
In a typical brewing process (Figure 1) lubricant contamination control points exist, which impose severe lubrication requirements that have not been met well by traditional white oil based food grade lubricants. Use of synthetic Poly Alpha Olefin (PAO) based food grade lubricants in these applications however has been proven to be effective in improving the life of the lubricant and the equipment when compared to white oil Food grade lubricants reducing the need for planned and unplanned shutdowns.
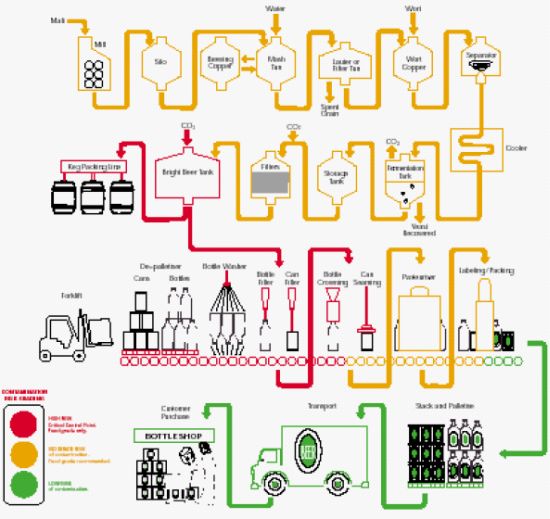
Fig. 1: Contamination Risk in the Beer Manufacturing Process
Better performance
Why do PAO Synthetics generally perform better?- They do not suffer from being compromised by extra refining which removes the "good" ingredients e.g. Natural anti-oxidants; Sulphur compounds (anti-wear & anti-oxidant)
- They’re designed for higher performance; they’re inherently more stable at high temperature with better oxidation stability, shear stability and thermal stability.
- They respond much better to additives; i.e. additives at same concentration tend to give better performance in synthetic base fluid than in mineral oil
- More/different additives are needed to boost the performance of mineral white oil but
- FDA restricts the choice and concentration of additives, so mineral white oil H1 products equals lower performance
![]() |
More/different additives are needed to boost the performance of mineral oil but FDA restricts the choice of additives, so mineral oil H1 products have LOWER performance |
Fig. 2: Food grades - White Oil versus PAO performance levels
Case studies and examples
Synthetic PAO based food grades offer opportunities for breweries to rationalise their product range by the nature of their superior performance replacing non food grade lubricants. In one example, an Australian brewer was able to rationalise their range of lubricants used from 37 to 10.In case studies, synthetic PAO based food grade lubricants have been shown to increase the life of the equipment and the lubricant when compared with mineral oil based food grade lubricants and mineral oil non food grade lubricants. Using synthetic PAO based food grade lubricants in lubricant contamination control points not only makes sense in terms of protecting against chemical contamination but also in terms of plant productivity.
Crown Capping Assembly
The rotary reciprocating action of the crown capping assembly is a pure sliding action, the most difficult lubrication regime to counter. Using a PAO based food grade grease (Shell Cassida Grease RL2) an Australian Brewery was able to extend maintenance on the machine from once per shift to once per day because of the superior wear rates when compared with white oil based Food grade lubricants.Can Seaming
With the major equipment manufacturers offering canning machines with speeds of 3000 cans per minute, the lubrication requirements of the seaming turret is possibly the most demanding of the entire process. Can seaming lubricants which may be oil or grease based must be H1 quality as they are likely to be in direct contact with the beer. Use of synthetic PAO based food grade lubricants has extended the life of the lubricant and equipment dramatically.![]() |
In a particular case study, Angelus machines have operated more than 16,000 hours without an oil change using the PAO based Shell Cassida Fluid GLE... Angelus now recommends using the synthetic PAO based Shell Cassida Fluid GLE 150 and Shell Cassida Fluid GLE 220 and Shell Cassida Grease RL 0 and Shell Cassida Grease RL 2 in its machines. |
Fig. 3: Angelus Seaming Machine - 16,000 hours without an oil change |
Chains and Conveyors
Chain lubrication is needed mainly to slow the wear between the pins and bushings in the chain joints, inhibit rust and corrosion, carry away heat, and flush out debris and foreign materials. Lubrication in itself maintaining low wear also cushions impact forces and smooths the chains engagement with the sprocket. In high speed environments with low tolerances of alignment with items such as hydraulic or actuated rams and filling nozzles, smooth engagement of the chain and sprocket becomes an important consideration to ensure filling and packaging lines function smoothly over long runs. As the chain wears well before the actual life of the chain is reached, a lubricant that promotes low wear levels is necessary. Synthetic PAO based Food grade lubricants have a much lower level of wear than white oil based Food grade lubricants and ensure not only longer equipment life but in addition, smoother operations of high speed equipment.Gearboxes
Gearboxes in breweries attached to chain drives, conveyor drives, mixers and agitators suffer the problems lubricating gearboxesIn a case study, synthetic PAO based Shell Cassida GL220 lasted well in excess of 2000 hours in a Westfalia separator gearbox. |
typical of any factory. That is, misalignment, high-speed and overloading causing higher running temperatures, which may cause premature ageing of gear oils and the leakage of greases lubricating the bearing supporting the main drive shaft. Most breweries need to limit the oil change interval to no less than 2000 hours to limit downtime. This puts even more stress on the oil.
A further problem is the location of the gearbox relative to the rest of the processes. Gearboxes positioned, for instance, above a mashing vessel run the risk of lubricants dripping in small quantities from a gearbox into the vessel. Selection of appropriate H1 oils and greases is necessary. By choosing synthetic PAO based Food grade oils and greases maximum protection is gained as their higher film strength at higher operating temperatures tends to reduce the operating temperature when compared to standard mineral oil based lubricants.
The opposite of course occurs when the gearbox is positioned below the rest of the processes, for example rinsing and can seaming, where the beer, its components or wash down water may leak in small quantities into the gearbox. A simple way of countering this problem is to introduce above the level of the oil in small positive air pressure (15 to 20 kpa), which will prevent any fluid ingress through the seal around the drive shaft.
Air compressors
A contamination risk which is usually hidden is the use of compressed air. For example, during the malting process compressed air is used to assist in the movement, drying, cooling, germination and kilning of malt. It is used in depalletising, rinsing, filling and palletising equipment. Typical breweries will have multiple numbers of air compressors with the rotary design being most popular. Oil injected as a mist into the compressor to lubricate it is removed on the exit side by a coalescer filter. However, it impossible to remove all of the oil mists. Oil remains in the air at concentrations of 30 to 300 parts per million (ppm). Secondary air filters may be used to further reduce the concentration. The actual concentration of oil in the air in a specific brewery will depend on the condition of the compressor, the condition of the coalescer filter, whether secondary filters are used and the performance of the compressor oil.In general air compressors consume too much oil3. The oil consumption in some cases may be reduced by 50% by using high performance oils and adopting good maintenance practises. The cost of lubricants is about 1% of the total compressed air cost. Unsuitable oils can increase this to as much as 5%.
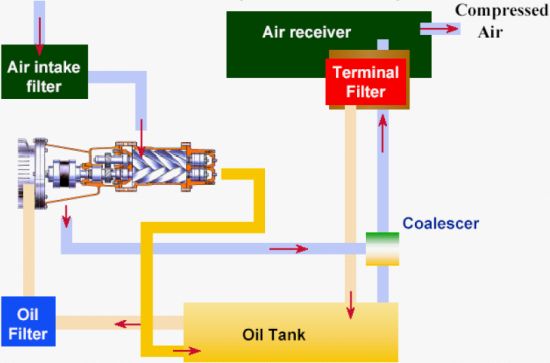
Fig. 4: Air compressor setup
Compressors are usually lubrication critical control points and food grade oils must be used except for oil free compressors. (Although Hitachi recently approved Shell Cassida CR46 for use in their oil free compressors). Using mineral food grade oil is not enough. Synthetic food grade oils significantly reduce oil mist in compressed air and improve food safety. It also saves overall cost as all oil and equipment lines are longer.
In one case study an Atlas Copco GA37 screw compressor with a norma oil change interval of 4,000 hours ran to over 5,800 hours on synthetic food grade oil. The coalescer and oil filter were inspected and both were found to be clean and free from deposits. The seals were in excellent condition. Oil analysis showed that the oil was still in excellent condition and could have lasted longer. | |
Atlas Copco oil-flooded GA37 screw compressor, after 5756 hr | |
![]() |
![]() |
Clean Coalescer: will remove oil mist efficiently | Oil filter Mounting plate: no sign of oil oxidation |
Fig. 5 Atlas Copco Screw Compressor after 5756 hours |
In comparison with synthetic PAO based food grade lubricants White Oil based food grade lubricants tend to oxidise more easily. This results in larger mist droplets, which leads to less efficient cooling of the compressor. The higher temperature further increases the oxidation level of the oil. Oxidised oil deposits gum and lacquer on the coalescer thereby reducing its efficiency and consequent air quality by clogging the filter. Furthermore, if compressor parts are worn, there is more oil mist in the compressed air which tends to saturate the coalescer filter.
Beer Foam Stability
For beer drinkers undoubtedly one of the more important characteristics of a beer is the stability of the foam. Some lubricants which may come in incidental contact with beer whilst meeting NSF H1 requirements when present in beer at or near the maximum of 10ppm will cause a severe reduction in foam stability. Products such as the Shell Cassida range which are composed of synthetic PAO base fluids maintain good beer foam stability (Figure 6) even at 10ppm.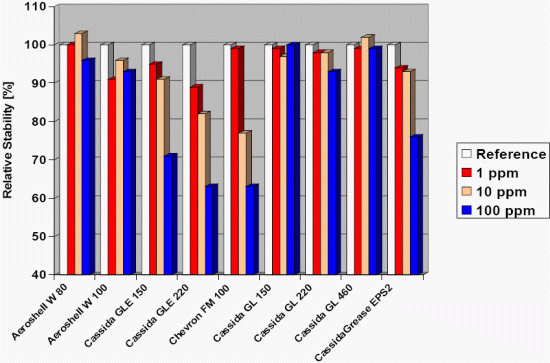
Fig. 6: Beer foam stability by the Rudin method
Conclusion
Modern brewing companies are under increasing pressure to work at higher speeds of production with lower levels of downtime. Faster speeds are causing equipment to run at higher temperatures. The lubricants they use are required to operate in ever more hostile environments for longer. The dilemma is that traditional food grade lubricants cannot meet the requirements and breweries run the risk of diminishing their reputation by using lubricants which do not comply with NSF H1 in areas which may come into incidental contact with beer. Synthetic PAO food grades offer solutions to this dilemma giving modern breweries an opportunity to not only protect their brand reputation through reducing contamination risk but can now deliver reduced down time and improved productivity and costs as well.1 Brewer's Handbook (Ted Goldammer)
2 Article 3(2) of Directive 93/43/EEC
3 Compressed Air and Gas Handbook (L. Engel)
Para más información: FUCHS LUBRICANTS GmbH